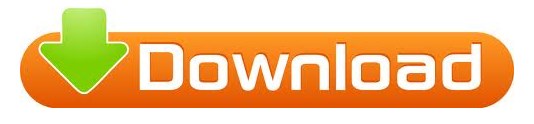
#STEP 7 5.5 FB12 FREE#
– Display of the reserved and free memory. – Display of cycle duration (longest, shortest and last cycle). – Causes of malfunction during user program execution. – Display of alarms from the diagnostics bufferįor CPUs, additional information is displayed: – Display of module faults (e.g., channel faults) of thecentral I/O and DP slaves – Display of general module information (e.g., order number,version, designation) and module status (e.g., faulty) – Pixel-graphics display within the Hardware Config display,offering the following options: – Display of text messages, which can be output directly andquickly. The display can be in two different forms: System diagnostics offer the user an overview of the status of theautomation system. – Parameterization of the selected communication blocks in thecustomary programming – Selection of the communication function blocks (CFBs) from theintegrated block library.
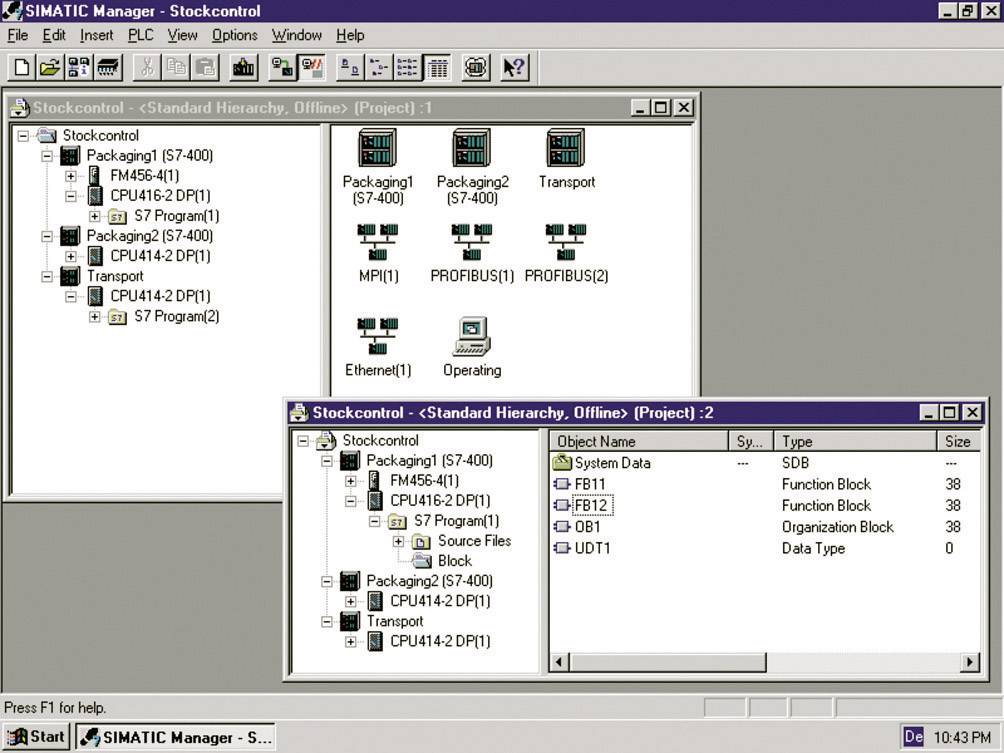
– Parameterization of the selected communicationblocks in the customary programming language (e.g., LAD). – Entering of data source and data destinationin a table.Generation of all system data blocks (SDBs) to be loadedand their complete transmission to all CPUs take placeautomatically – Time-driven cyclic data transmission via MPI: – Configuring and display of communication links The system prevents faulty inputs by offeringonly allowed entry options on the parameter assignment screenforms. Forthis parameterization hardware-module-specific screen forms andrules are provided for each FM and CP (is included in the FM/CPfunctions package). This parameterization also occurs within the hardware configurationin the same way as the parameterization of the other modules. – Function module (FM) and communications processor (CP) parameterassignment: Thus, a change of amodule can be made without another parameterization. Parameterization of hardware modules occursautomatically during the CPU’s acceleration. Adjustments via DIP switches becomeunnecessary. The user can specify all the adjustable parameters of the modulesin input screen forms. Theentered data are filed in system data blocks in the CPU. Properties such as restart characteristics and cycle-timemonitoring can be set menu-driven. – The configuration of the distributed I/Os is done in the same wayas the configuration of the non-distributed I/Os channel-granularI/O modules are also supported. – Configuration of the automation system Racks are selectedfrom an electronic catalog and the selected modules are assigned tothe required slots in the racks. The tool Hardware Configuration is used for configuring andparameterizing the hardware used for an automation project. Changes to a symbol parameterare therefore automatically recognized by all tools.
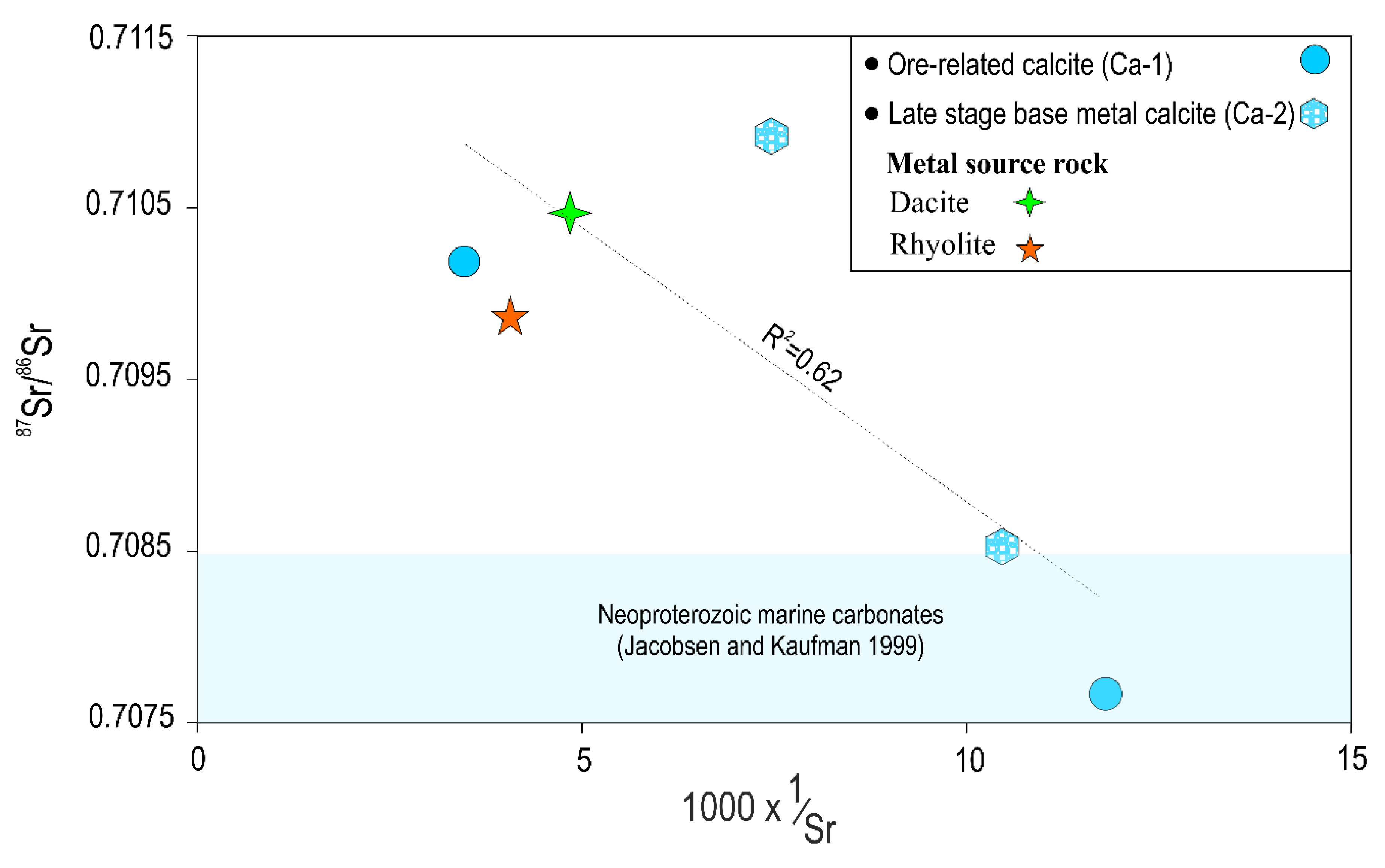
#STEP 7 5.5 FB12 SOFTWARE#
The symbol charts that are generated when this tool is used areavailable to all software products.
#STEP 7 5.5 FB12 WINDOWS#
– Data exchange with other Windows programs – Definition of symbolic designations and comments for the processsignals (inputs/outputs), flags and blocks With the tool Symbol Editor all global variables (in contrast tothe local formal parameters that are declared when the blocks areprogrammed) are managed. The SIMATIC software tools that are necessary for processingthe selected data are automatically started by SIMATIC Manager. It provides a common entry point for all SIMATIC S7, C7 or WinACtools.

The SIMATIC Manager manages all data belonging to an automationproject, regardless of the target system (SIMATIC S7, SIMATIC C7 orSIMATIC WinAC) on which they are implemented.
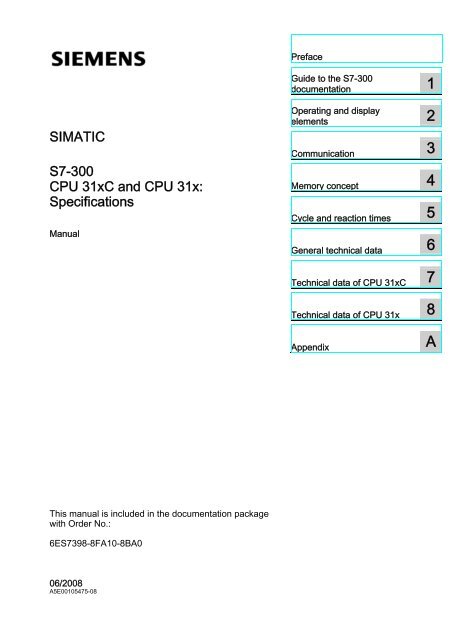
– Configuring and parameterizing the hardware SIMATIC STEP 7 contains convenient functions for all phases of anautomation project: It enables the user to use the performancecapability of these systems easily and conveniently. Siemens SIMATIC STEP 7 software is theprofessional tool for the SIMATIC S7, SIMATIC C7 and SIMATIC WinACautomation systems.
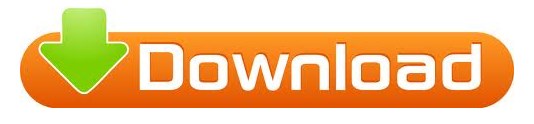